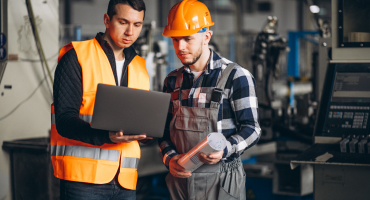
Modern Technology
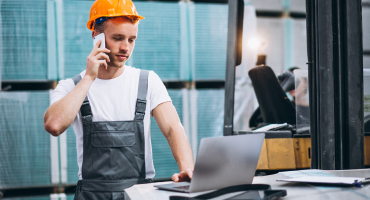
Fully Integrated
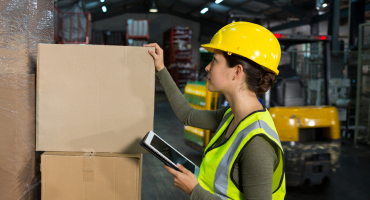
Dynamic Automation
In today’s fast-paced world with booming eCommerce, customers expect on-time delivery of products ordered from your online store. Designed for speed, P4Warehouse allows you to get your order to the customer without any delay.
The order accuracy rate is important since it correlates directly with customer support inquiries, and even the quantity of eCommerce exchanges and returns you receive. Moreover, order accuracy will impact customer loyalty and follow up orders.
The process in a warehouse that occurs after an order is placed from an online store is called pick and pack fulfillment. To reduce costs, we have streamlined the process with our WMS. The WMS generates automated picking lists, tracking customer orders, and guiding the pickers. Our WMS enables us to find the individual items on the picking list and to find the correct quantities from their location in the warehouse.
With our WMS we can provide boxes with the best fit for your order. Discrete picking is best for small businesses with low SKU counts and your orders can be sent out in batches to be picked on one walk through the warehouse
However, when you have many identical orders that use the same SKUs batch picking (cluster picking) works best. It allows a picker to stay in the same area avoiding traveling long distances across the warehouse. By reducing repeated trips, steps, and time, batch picking reduces costs and improves productivity.
When pickers are assigned to a physical area of the warehouse, where they only pick SKUs in that zone, it is called Zone picking (“pick and pass”).
Errors are reduced since a single picker can become familiar with the items in his zone Therefore, the picker does not have to try learning the ins and outs of the entire warehouse.
Managing complex products or a large range of SKU’s used to require significant investments in software. Using a proper WMS allows you to increase efficiency and reduce costs.
Consequently, P4Warehouse will handle all your inventory requirements. Not only is it able to handle any type of product from decimal to multi-pack sized, but it will also empower you to be live in just months.
Inventory management is more than just organizing products. Inventory visibility is achieved through the right alignment of network strategy, facility and process engineering, and technology systems. Inventory visibility allows you to deliver to your customer through their preferred sales channel at a cost ratio that serves your bottom line.
The aim is to have the right quantity of inventory/stock at hand when it is required. Therefore, inventory management is the process of organizing and tracking all the company's goods during the time the company owns them.
Inventory management is also equated to stock management in some industries in the retail sector, where they are considered as “stock on hand”. Consequently, the quantity of inventory that will be carried by a company will depend on many factors. The production time of a product will determine whether the product will be carried in the inventory or whether it will be operated on a just-in-time basis.
P4Warehouse WMS allows you to keep a count of products and provide actionable business intelligence including the identification of low and high-performing products. Moreover, it will automatically send re-order notifications when stocks are low. With accurate inventory information, managers have more confidence to make purchasing and sales decisions.
P4Warehouse WMS allows you to keep a count of products and provide actionable business intelligence including the identification of low and high-performing products. Moreover, it will automatically send re-order notifications when stocks are low. With accurate inventory information, managers have more confidence to make purchasing and sales decisions.
Through the integration of the information, the dashboards allow you to Extract, Load, and Transform (ELT) all transactional information. ELT involves gathering transactional data from the applications’ database (extract), converting it into reportable data (transform), and storing it in a data warehouse (load).
Our WMS dashboard allows you to transform and intergrade data from different data sources to provide you a better picture of your business. Consequently, it results in all customer information being reported. It ensures all data relating to customer invoices are included in the report. Therefore, there are no gaps and unanswered questions.
Our dashboards do not only provide you with a current transactional view. The processes allow you to merge and interpolate historical information to provide you with an overall view of trends and how it has changed over time.
Furthermore, our dashboards allow data reports to be run on a schedule or ad-hoc basis from all business systems. Consequently, it removes the time and effort you spend on creating reports. The reports, therefore, eliminate human error, and that the resulting reports are accurate and trusted.
The reports generated through the dashboards provide clear guidance for recommended levels of safety stock, customers, and fulfillment strategies. It provides a tool for understanding demand and how to position yourself to provide a high-quality customer service experience.
Beyond eCommerce, SAP, and accounting integrations, P4Warehouse has a restful API to manage integrations with the tools you already use. Overall, more integrations result in better data flow and less human error. It is therefore beneficial integrating where one can.
Integrating software provides you with the ability to manage the fulfillment of your orders in real time. It provides real time sales reporting, offering all sorts of opportunities for business intelligence. It allows more accurate tracking of inventory levels, limiting backorders. Most importantly, it provides real time alerts when stock gets low.
Integration of software allows quicker processing, which gets orders to the warehouse floor more quickly and makes two-day shipping windows possible. Furthermore, it assists to set up deals and promotions right in the shopping cart, to enable you to move slow moving inventory/stock.
The integration of systems allows you to stay on top of put away, vendor returns, good receipts, picking, ordering, replenishment, local management, and reporting on physical and cycle counts. This real time information will boost your company’s efficiency and provide you with the answers you require when you need them.
The integration of your WMS and ERP systems are important, allowing access to the information you need to make business decisions. If your sales team has access to information in your warehouse management system, they can effectively update customers on order status. Integration creates a seamless connection between systems ensuring that no one in your company is out of the loop. This sharing of information between platforms ensures that your sales team does not over commit, and that management always have a clear picture of your supply chain.
The integration of your WMS and ERP systems are important, allowing access to the information you need to make business decisions. If your sales team has access to information in your warehouse management system, they can effectively update customers on order status. Integration creates a seamless connection between systems ensuring that no one in your company is out of the loop. This sharing of information between platforms ensures that your sales team does not over commit, and that management always have a clear picture of your supply chain.
With the advent of e-commerce, shipping is a crucial part of the logistical management of your inventory. Shipping does not only affect customer satisfaction, but it also affects the bottom line of your pricing across the board. With our WMS Compare pricing for shipping across the systems and make the best decision each time.
Some customers want partial shipments whilst others require full shipment. Our WMS caters for the full range of shipping variations to ensure you achieve customer satisfaction. Consequently, if you do not have full stock to fulfill a shipment our WMS allows you to send a partial shipment. Moreover, if you have many orders and do not have sufficient stock to allocate to them, you can balance the stock across a few customers. Therefore, using our WMS, you can allocate the stock you have and ship partial, following-up with additional shipments to complete your customers orders.To enable you to ship to your customers at the announced times, our WMS advanced functionality allows you to coordinate between sales, warehouse, and accounts receivable teams and to coordinate seamlessly with the order, ship, and invoicing processes.
Business users in various parts of the world expect to be able to use computer code and applications, as well as business intelligence, in their own language to enable them to achieve higher productivity. This method is supported by activities, processes and applications that are collectively referred to as business intelligence. Business Intelligence initially described activities and tools related to the reportage and analysis of information available in data warehouses.
To survive and compete in the current competitive environment you should on a continuous basis increase productivity and efficiency throughout the business. This means that business information from all the warehouse processes should be available to all the teams in their own language. Managers needs to interpret the business information while management and executives must make decisions derived from interpreting the business information almost immediately to ensure competitiveness.
Multilingualism is further justified by the importance of rising markets, changing attitudes of business users, and expanding local data warehousing communities. The design and reporting functions in warehouse management presents unique challenges for multilingualism.
With these challenges in mind P4 warehouse designed a multilingual, scalable international warehouse management system, for managing your warehouse and distribution centers. Most importantly, the multilanguage functionality is available to be used throughout the whole process from sales, warehouse, and accounts receivable to the order, ship, and invoicing processes.
With our WMS all business information can be accessed in your preferred language and extrapolated to create reports that will enable you to make the business decisions that will give you the edge above your competitors.
In today’s fast-paced world with booming eCommerce, customers expect on-time delivery of products ordered from your online store. Designed for speed, P4Warehouse allows you to get your order to the customer without any delay.
The order accuracy rate is important since it correlates directly with customer support inquiries, and even the quantity of eCommerce exchanges and returns you receive. Moreover, order accuracy will impact customer loyalty and follow up orders.
The process in a warehouse that occurs after an order is placed from an online store is called pick and pack fulfillment. To reduce costs, we have streamlined the process with our WMS. The WMS generates automated picking lists, tracking customer orders, and guiding the pickers. Our WMS enables us to find the individual items on the picking list and to find the correct quantities from their location in the warehouse.
With our WMS we can provide boxes with the best fit for your order. Discrete picking is best for small businesses with low SKU counts and your orders can be sent out in batches to be picked on one walk through the warehouse
However, when you have many identical orders that use the same SKUs batch picking (cluster picking) works best. It allows a picker to stay in the same area avoiding traveling long distances across the warehouse. By reducing repeated trips, steps, and time, batch picking reduces costs and improves productivity.
When pickers are assigned to a physical area of the warehouse, where they only pick SKUs in that zone, it is called Zone picking (“pick and pass”).
Errors are reduced since a single picker can become familiar with the items in his zone Therefore, the picker does not have to try learning the ins and outs of the entire warehouse.
Managing complex products or a large range of SKU’s used to require significant investments in software. Using a proper WMS allows you to increase efficiency and reduce costs.
Consequently, P4Warehouse will handle all your inventory requirements. Not only is it able to handle any type of product from decimal to multi-pack sized, but it will also empower you to be live in just months.
Inventory management is more than just organizing products. Inventory visibility is achieved through the right alignment of network strategy, facility and process engineering, and technology systems. Inventory visibility allows you to deliver to your customer through their preferred sales channel at a cost ratio that serves your bottom line.
The aim is to have the right quantity of inventory/stock at hand when it is required. Therefore, inventory management is the process of organizing and tracking all the company's goods during the time the company owns them.
Inventory management is also equated to stock management in some industries in the retail sector, where they are considered as “stock on hand”. Consequently, the quantity of inventory that will be carried by a company will depend on many factors. The production time of a product will determine whether the product will be carried in the inventory or whether it will be operated on a just-in-time basis.
P4Warehouse WMS allows you to keep a count of products and provide actionable business intelligence including the identification of low and high-performing products. Moreover, it will automatically send re-order notifications when stocks are low. With accurate inventory information, managers have more confidence to make purchasing and sales decisions.
P4Warehouse WMS allows you to keep a count of products and provide actionable business intelligence including the identification of low and high-performing products. Moreover, it will automatically send re-order notifications when stocks are low. With accurate inventory information, managers have more confidence to make purchasing and sales decisions.
Through the integration of the information, the dashboards allow you to Extract, Load, and Transform (ELT) all transactional information. ELT involves gathering transactional data from the applications’ database (extract), converting it into reportable data (transform), and storing it in a data warehouse (load).
Our WMS dashboard allows you to transform and intergrade data from different data sources to provide you a better picture of your business. Consequently, it results in all customer information being reported. It ensures all data relating to customer invoices are included in the report. Therefore, there are no gaps and unanswered questions.
Our dashboards do not only provide you with a current transactional view. The processes allow you to merge and interpolate historical information to provide you with an overall view of trends and how it has changed over time.
Furthermore, our dashboards allow data reports to be run on a schedule or ad-hoc basis from all business systems. Consequently, it removes the time and effort you spend on creating reports. The reports, therefore, eliminate human error, and that the resulting reports are accurate and trusted.
The reports generated through the dashboards provide clear guidance for recommended levels of safety stock, customers, and fulfillment strategies. It provides a tool for understanding demand and how to position yourself to provide a high-quality customer service experience.
Beyond eCommerce, SAP, and accounting integrations, P4Warehouse has a restful API to manage integrations with the tools you already use. Overall, more integrations result in better data flow and less human error. It is therefore beneficial integrating where one can.
Integrating software provides you with the ability to manage the fulfillment of your orders in real time. It provides real time sales reporting, offering all sorts of opportunities for business intelligence. It allows more accurate tracking of inventory levels, limiting backorders. Most importantly, it provides real time alerts when stock gets low.
Integration of software allows quicker processing, which gets orders to the warehouse floor more quickly and makes two-day shipping windows possible. Furthermore, it assists to set up deals and promotions right in the shopping cart, to enable you to move slow moving inventory/stock.
The integration of systems allows you to stay on top of put away, vendor returns, good receipts, picking, ordering, replenishment, local management, and reporting on physical and cycle counts. This real time information will boost your company’s efficiency and provide you with the answers you require when you need them.
The integration of your WMS and ERP systems are important, allowing access to the information you need to make business decisions. If your sales team has access to information in your warehouse management system, they can effectively update customers on order status. Integration creates a seamless connection between systems ensuring that no one in your company is out of the loop. This sharing of information between platforms ensures that your sales team does not over commit, and that management always have a clear picture of your supply chain.
The integration of your WMS and ERP systems are important, allowing access to the information you need to make business decisions. If your sales team has access to information in your warehouse management system, they can effectively update customers on order status. Integration creates a seamless connection between systems ensuring that no one in your company is out of the loop. This sharing of information between platforms ensures that your sales team does not over commit, and that management always have a clear picture of your supply chain.
With the advent of e-commerce, shipping is a crucial part of the logistical management of your inventory. Shipping does not only affect customer satisfaction, but it also affects the bottom line of your pricing across the board. With our WMS Compare pricing for shipping across the systems and make the best decision each time.
Some customers want partial shipments whilst others require full shipment. Our WMS caters for the full range of shipping variations to ensure you achieve customer satisfaction. Consequently, if you do not have full stock to fulfill a shipment our WMS allows you to send a partial shipment. Moreover, if you have many orders and do not have sufficient stock to allocate to them, you can balance the stock across a few customers. Therefore, using our WMS, you can allocate the stock you have and ship partial, following-up with additional shipments to complete your customers orders.To enable you to ship to your customers at the announced times, our WMS advanced functionality allows you to coordinate between sales, warehouse, and accounts receivable teams and to coordinate seamlessly with the order, ship, and invoicing processes.
Business users in various parts of the world expect to be able to use computer code and applications, as well as business intelligence, in their own language to enable them to achieve higher productivity. This method is supported by activities, processes and applications that are collectively referred to as business intelligence. Business Intelligence initially described activities and tools related to the reportage and analysis of information available in data warehouses.
To survive and compete in the current competitive environment you should on a continuous basis increase productivity and efficiency throughout the business. This means that business information from all the warehouse processes should be available to all the teams in their own language. Managers needs to interpret the business information while management and executives must make decisions derived from interpreting the business information almost immediately to ensure competitiveness.
Multilingualism is further justified by the importance of rising markets, changing attitudes of business users, and expanding local data warehousing communities. The design and reporting functions in warehouse management presents unique challenges for multilingualism.
With these challenges in mind P4 warehouse designed a multilingual, scalable international warehouse management system, for managing your warehouse and distribution centers. Most importantly, the multilanguage functionality is available to be used throughout the whole process from sales, warehouse, and accounts receivable to the order, ship, and invoicing processes.
With our WMS all business information can be accessed in your preferred language and extrapolated to create reports that will enable you to make the business decisions that will give you the edge above your competitors.